introduction
Industrial Ethernet has become the mainstream technology for factory automation for a variety of reasons. What did not receive the same attention was the need to implement this communication technology in the supplier system. In fact, how you can achieve this demanding feature will vary greatly in terms of system cost, product form factor, and power consumption metrics. This article introduces the various options for implementing Industrial Ethernet, such as I/O modules and drive slave systems, from the perspective of factory automation suppliers developing slave systems.
The challenges faced by these OEMs are not common, so there are good reasons to check the slave system architecture. The vendor does not design a slave system for a certain protocol. They must support any standard that can be implemented in the factory, not a single protocol. Their systems must adapt to any kind of agreement.
The new standard for developing slave protocols also has unique hardware features. In fact, they can't use standard MAC implementations, which face rare challenges that affect the choice of implementation platform.
Industrial Ethernet Introduction
In the beginning, Ethernet—10 Mbps of initial Ethernet, 100 Mbps of Fast Ethernet, and 1 Gbps of Gigabit Ethernet—transmit signals between devices on a shared medium that are not suitable for industrial applications. With the advent of Fast Ethernet (100 Mbps), its switching mode supports full-duplex capability, meaning that point-to-point links can be built between two devices, enabling Ethernet to be used in most industrial applications. All Industrial Ethernet protocols require a certain degree of judgment, traditionally solved by using a software protocol stack.
Speed ​​requirement (or delay in this case)
We all know that factory automation systems have real-time response requirements. So, what is “real time� The answer is that it depends on the type of application. Sometimes, measured in hundreds of milliseconds, and sometimes measured in microseconds. There are different design methods that enable communication protocols to meet different latency requirements.
As shown in Figure 1, the PHY layer is usually a separate analog device. However, other functions can be implemented in the digital logic device, with the processor running the software for the protocol stack as well as the custom application. All industrial Ethernet protocols require a special software stack, and some new protocols (shown on the right side of the figure) use a unique, non-standard design for media access control (MAC) and switching.
Figure 1. Industrial Ethernet Protocol Architecture
EtherCAT and Profinet IRT are two newer protocols that require a special MAC design. In particular, EtherCAT uses an innovative approach to encapsulating more packets in an Ethernet frame. Data from multiple slave devices is encapsulated into an Ethernet frame. When a slave device reads an Ethernet frame, it must extract the intrinsic meaning of the packet for itself, ignoring other information. More importantly, it must do this extraction at any time.
When many slave devices are connected, the data packets are extracted to meet the minimum latency requirements. For example, if you are the 256th slave device on the network, it will cause a frame delay instead of a 256 frame delay. Typical applications are motion control and multi-axis robotic drive.
To support the chosen protocol, the MAC design in the slave device is different from the traditional Ethernet MAC and requires special design in the FPGA or ASIC. From a system design perspective, if you must support standard MAC implementations and special implementations, the design should include a MAC design or be hardware programmable. Figure 2 shows how different real-time requirements lead to different architectures for communication protocol standards.
Figure 2. Different real-time requirements lead to different implementations
Key trends affect system design
Some of the trends affecting industrial Ethernet system design include embedded communication protocols, the rapid development of industrial Ethernet standards, and the development of Gigabit Ethernet.
Embedded communication protocol
The first trend in drive and I/O modules (typical slave devices in factory automation) is the deep embedding of communication functions due to factors such as reduced system cost, reduced form factor, and reduced power budget. In the past, customers spent hundreds of dollars to purchase commercial communication modules and then added them to the driver module. These modules are not cost effective and are not suitable for small form factor package drive designs. Another alternative is to include a separate ASSP dedicated to implementing communication functions. Because different customers use different Industrial Ethernet standards, this ASSP may be over-engineered to support multiple protocols.
However, vendors want to integrate all of their digital drive functions into a single silicon chip, requiring communication protocols that are small in scale and can be implemented as part of a complete "chip-driven" system. Figure 3 shows the transition in the implementation of Industrial Ethernet functionality.
Figure 3. From module to device to chip integration
Rapid development of industrial Ethernet standards
The second trend is the rapid development of industrial Ethernet standards. Similar to the fieldbus protocol, there are many types of Industrial Ethernet protocols and, most importantly, these standards are not combined in the market.
Driver system suppliers must be able to support six to eight standards in order to sell their products to different plants around the world.
For example, if you want to sell your drive equipment in Asia and Europe simultaneously, and adapt to Ethernet POWERLINK and EtherCAT, you need to: 1) design, develop, and maintain two sets of drive designs; or 2) include ASSPs to support multiple Protocols - hope that the agreement will not change; or 3) use programmable platforms Table 1 lists some of the competing Ethernet standards that are popular around the world.
Table 1. Competitive Ethernet standards based on the underlying fieldbus protocol
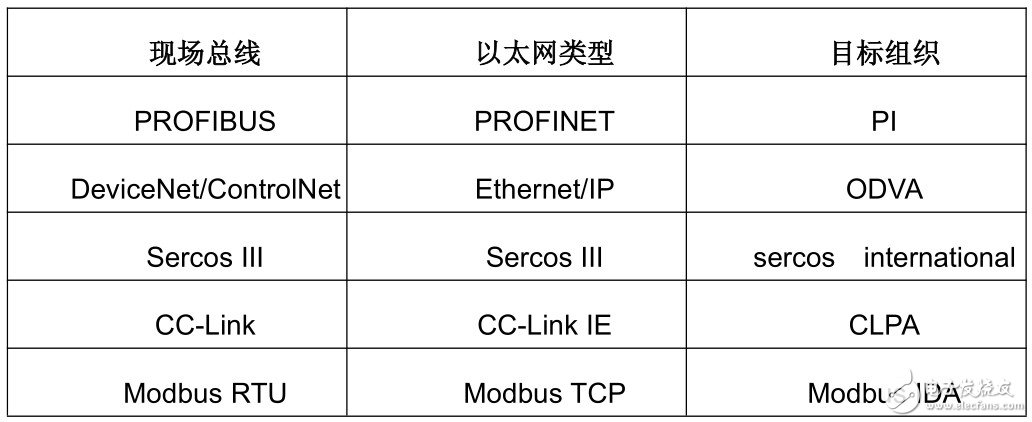
In the past, when the Industrial Ethernet standard used standard MAC/switching, it was easy to use a microprocessor unit (MPU) for communication. If you need to support the new standard, you only need to exchange the protocol stack (software). However, as discussed earlier, many new standards require special MAC implementations. Obviously, when dealing with these new standards, it is not enough to standardize the communication protocol with standard Ethernet MACs and switches on standard MPUs.
Some MPU vendors have developed new methods, such as developing custom microcode for use with dedicated embedded processors for emulating non-standard MACs. But these are very esoteric methods and there may be defects that are not known. Protocols that require a special MAC implementation typically use a custom hardware approach that uses an ASIC or FPGA depending on the yield and the required price point.
In addition, MAC design is always possible to change as standards evolve. To ensure that your design will not become obsolete in the future, it is safest to use a programmable method.
Chinese Tier 1 brand Solar Panel (Longi, Jinko, Trina, Canadian, Ja etc.)
This type of product is mainly Tier 1 solar module product in China, include Longi solar panel. Jinko solar panel, Canadian Solar panel, ja solar panel etc.all of which are among the top 10 world-renowned brands. The original A grade product is mainly mono crystalline and half cut cell solar modules, with a power range of 400watts to a maximum of 700watts.quality warranty is 25 years.
A grade, this type of film is characterized by a neat and uniform appearance, printed electrode grid lines, no broken grid, no surface stains, no leakage, no aluminum package, no hidden cracks, no scratches, no black core, no reverse current, stable electrical performance, and high conversion efficiency
Using solar cell testing equipment to measure and screen, the conversion efficiency, filling factor, and appearance that meet certain standards are first level. Generally, the conversion efficiency, filling factor, and appearance of first level are better than those of level B
The level of solar panels can be divided into first level, second level, third level, and fourth level, and the first level components can be divided into first level+and first level - two levels. The second level is also the same, and the cost difference between different levels of solar panels is also very large.
Chinese tier 1 brand solar panel
TIER 1 brand include
Longi, Jinko, Trina, JA, Canadian, znshine, etc.
quality warranty
25 years
grade
original A grade (each solar panel can be checked on official website with barcode)
power range
400watt to max 700watt
Tier 1 Solar Panel,Mono Solar Panel N Type,Solar Panels Bifacial 555 Watt,Solar Panel Mono Topcon Cell
PLIER(Suzhou) Photovoltaic Technology Co., Ltd. , https://www.pliersolarpanel.com