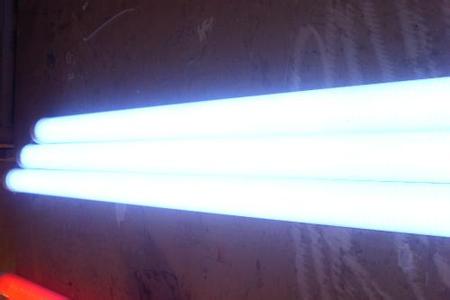
High-power white LEDs are used in everyday lighting applications. In fact, environmental protection light sources have become increasingly important. They have become the primary choice for the development of environmentally friendly light sources. However, in reality, there are still many technical bottlenecks in white LEDs that have yet to be overcome. Currently, there are related improvements to enhance the design of white LEDs in terms of uniformity of light emission, lifetime of packaging materials, and enhancement of heat dissipation, and to carry out key functions and performance. Improvements.
Increased demand for environmentally-friendly light sources The main reason why high-power white LED applications are suitable for out-of-line LED light sources is their long life, high light-to-electricity conversion efficiency, and the characteristics of materials that can be mounted on arbitrary planes. However, in the development of daily lighting sources, due to the need to achieve practical "lighting" requirements, the original LED with the indication can not directly correspond to lighting applications, must be strengthened from the chip, package, carrier board, production technology and external circuits, In order to achieve the high power, high brightness lighting effects required for lighting applications.
In terms of market demand, white LEDs developed for the lighting application market can be said to be products with higher usage in the future. However, in order to achieve utility, white LEDs must perform key function improvements for lighting applications. One is to strengthen the LED chip, for example, to increase its light-electricity conversion efficiency, or to increase the chip area, so that the amount of light emitted by a single LED (light flux) reaches its design limit. Second, it belongs to a more compromised design scheme. If it is difficult to continuously increase the area of ​​a single LED chip, use multiple LED chips to be packaged in the same light source module, which is a practical technical solution that can achieve the aforementioned method. .
To meet the requirements of low-cost, high-brightness design requirements for multi-chip packaging, industry practice requirements have been reviewed. Due to mass production flexibility, design difficulties, and control product yield/cost issues, LED chips continue to encounter design bottlenecks in which cost and yield are met. The design difficulties that may be encountered in increasing the chip area may not be met by technology and production technologies, but in terms of cost and efficiency, large-area LED chips have higher costs and changes in actual manufacturing requirements. Low design flexibility.
Instead, an integrated packaging method using a plurality of chips is used to arrange the plurality of LED chiplets on the carrier board in an equal distance, and the entire package of the chips and the optical package material is connected by wire bonding to form a light source module product. The chip package can be integrated into an equivalent large chip light source module after performing the chip test, but it is more flexible in terms of production flexibility than the monolithic design of the LED light source components.
At the same time, the cost of multiple LED chip module solutions can be significantly reduced due to the cost of the chip, which is equivalent to the lower cost of development options under the same luminous flux of the monolithic design.
Multi-chip integrated light source modules still need to consider the other cost-benefit maximization of another development direction is to continue to increase the LED chip area, through a large area to obtain high brightness, high luminous flux output effect. But too large LED chip area will also appear less than expected design problems, common improvement program is to modify the structure of the polycrystal, and make improvements on the surface of the chip; but the related improvement programs also easily affect the heat dissipation efficiency of the chip itself, especially in the light source. Most of the LED modules used require driving at high power to obtain higher luminous flux, which will cause the high heat collected by the chip junction during the light emission of the chip to not easily dissipate, affecting the application elasticity of the module product and the main/passive Thermal design.
In the general design scheme, the 7mm2 chip size is adopted for analysis, and the luminous efficiency is the best. However, 7mm2 large chips are less controllable in terms of yield and light performance, and the cost is relatively high. Instead, multichip chips are used, such as 4 The chip or 8 pieces of low-power chips for secondary processing to form a LED light source module on the carrier board with the package material is a design scheme of LED light source module products capable of rapidly developing desired brightness and power performance.
For example, manufacturers of light source products such as Philips, OSRAM, and CREE have introduced LED light source module products that integrate 4, 8 or more small LED chip packages. However, this type of high-brightness component scheme using multiple LED chip architectures also causes some design problems. For example, multiple LED chip combination packages must be combined with built-in insulating materials to avoid short-circuiting of individual LED chips; such a process is relatively There are many more programs in the monolithic design, so even if it can save cost compared to the monolithic solution, the cost gap between the two solutions can be reduced due to the additional insulating material process.
Application of chip surface process improvements can also enhance the LED light output In addition to increasing the chip area or number is the most direct method, there are also other light properties for the characteristics of the chip itself to improve light. For example, an uneven surface structure can be fabricated on an LED sapphire substrate, and the light output of the LED is enhanced by using the irregularly designed surface to create a textured surface crystallization structure on the surface of the chip.
OSRAM has used this solution to develop ThinGaN high-brightness products, forming a metal film material on the InGaN layer first, and then performing a peeling process, so that the peeled surface can indirectly obtain a higher light output! OSRAM claims this technology allows the same chip to achieve 75% light extraction efficiency.
On the other hand, the development thinking of Japan's OMRON is quite different, and the same is devoted to extracting the chip's light extraction efficiency. OMRON is trying to use the planar light source technology and LENS optical system to reflect, guide and control the chip light source, aiming at the traditional artillery shells. The light loss problem of the LED products of the package type structure further improves the design structure thereof, and the double-layer reflection effect is used to control and intensify the light extraction amount of the LED. However, this packaging technology is relatively more complicated and has a high cost. Therefore, it is mostly used only. In LCDTV backlight module design.
LED lighting applications still need to improve component light decay and lifetime issues If you look forward to LED light source into daily lighting applications, the application will need to overcome more problems! Because the daily lighting source has a long-term use situation, it often takes several hours or even tens of hours to turn on the LED. The LED that is turned on for a long time will cause the chip's light attenuation and lifetime reduction due to the high heat of the component. The component must propose a better solution for the heat treatment in order to slow down the premature failure of the light and affect the product experience.
Another big problem with the introduction of LED light sources into everyday applications is that, like conventional fluorescent lamps, the same luminous efficiency can be maintained for more than a few dozen hours, but the LEDs are different. Because the LED light emitting chip will cause its luminous efficiency to decrease due to high heat of the element, and this problem is no matter whether it is in high power or low power LED, but the low power LED is only used for indicative purposes, and the effect is very small for the user. However, if the LED is used as a light source, the problem of diminishing light output will be exacerbated by increasing the driving power of a single element for increasing the brightness. Generally, the brightness will drop after a few hours of use, and the heat dissipation design must be improved to achieve the light source. Application requirements.
LED packaging materials need to be improved due to high temperature and short-wavelength light. In the light source design, it is often used to increase the drive current in exchange for a higher light output of the LED chip, but this will increase the heat generated by the chip surface during the light emission process. The high temperature of the chip tests the durability of the package material. Under the condition of continuous high temperature operation, the original package material with high heat durability will deteriorate, and the material deterioration or quality change will further cause the light transmittance to decline. Therefore, the LED light source module is being developed. In the group, it is also necessary to use high heat-resistance materials in consideration of the packaging material.
There are many ways to increase the heat dissipation of the LED light source module components, which can be improved from the chip, the packaging material, the heat conduction structure of the module, and the design of the PCB carrier board. For example, if the heat transfer rate can be enhanced between the chip and the package material, it is also a method to rapidly dissipate the core heat source through the surface of the package material. Or by the contact between the chip and the carrier board, the core heat of the chip is directly transmitted through the direct conductive heat source of the material to the carrier board to disperse, and the focus of the LED chip heat is improved. In addition, the PCB adopts metal material matching and LED chip close assembly design, but also because of the reduction of thermal resistance of thermal conduction, to achieve the design goal of rapid dissipation of the core heat of the light-emitting components.
In terms of packaging materials, most of the LED components were encapsulated with epoxy resin in the past. In fact, the heat resistance of epoxy resin itself is not high, and often the LED chip has not been used for a long time. The epoxy resin has been heated for a long time. The discoloration phenomenon of deterioration and deterioration occurs during operation. In the LED module design of lighting applications, the speed of the packaging material is accelerated due to the high-power driving of the chip, and even the safety of the components is affected.
Not only high heat problems, such as epoxy resin plastic material, high sensitivity to light, especially short-wavelength light will cause destruction of epoxy resin material, and high power LED light source module, its short wavelength light There will be more, and there will be an increase in the rate of material deterioration.
For LED light source application design solutions, most of the companies tend to abandon epoxy resin encapsulation materials and switch to encapsulation materials that are more resistant to high temperatures and short-wavelength light. For example, tantalum resin has higher thermal resistance than epoxy resin, and In terms of material properties, lanthanum resins can achieve material advantages that do not change color in an environment of 150 to 180°C.
In addition, lanthanum resin can also be used to disperse blue light and ultraviolet light, and lanthanum resin can inhibit the problem of material deterioration due to high heat or short wavelength light in the packaging material, and slow down the decrease in light transmittance due to deterioration of the packaging material. As for the LED light source module, the lanthanum resin also has the advantage of prolonging the service life of the LED element, because the lanthanum resin itself has the advantages of high heat resistance and short-wavelength light resistance, and can protect the continuous high heat and light irradiation generated by the LED for a long time in the packaging material. Its relatively long life span also allows LED components to have a lifetime of more than 40,000 hours.
Ningbo Autrends International Trade Co.,Ltd. , https://www.mosvape.com